Plan for volume production of heat-resistant PLA gets underway in Japan
09 Jan 2009 • by Natalie Aster
A major drawback to the adoption of the biopolymer PLA – polylactic acid – has been its limited temperature and impact resistance. A number of manufacturers – notably in Japan where the government has a target of 20 per cent of all plastics used in the country coming from renewable feedstock by the late 2010s – have been working on higher-heat grades. One of them, the Teijin Group, is now moving into volume production with a target of 10,000 tonnes/year by 2010.
Teijin developed its Biofront PLA in association with Musashino Chemical Laboratory and produced fibres from it which were used by the Mazda car company for all the seating fabric in its Premacy Hydrogen RE Hybrid car introduced at the Tokyo Motor Show in 2007. Biofront is described as "a stereocomplex PLA made with high-purity L-lactate and D-lactate." It has a melting point of 210 degC, compared with the 170 degC melting point of conventional PLAs. Teijin is working to develop range of Biofront applications spanning fibres, films and moulding materials, with initial results in the apparel and automotive fields – following its seating fibre for Mazda Teijin is working on heat-resistant car interior trim. The company has also established injection-moulding technologies for pillar covers and centre console panels.
Future uses could include applications in the optical field: Teijin says Biofront transmits light more efficiently than PET.
At present Biofront is made on a 200 tonnes annual capacity pilot plant, but Teijin has recently acquired Toyota Motor Corporation's PLA demonstration plant with an approximate 1,000 tonne capacity which is expected to be making Biofront by the summer of this year. Development of the 10,000 tonnes plant is underway, as is research into how to use various non-edible bio-resources. Teijin is also exploring possibilities for the chemical recycling of used PLA products.
Source: Britishplastics.co.uk
Analytics & News
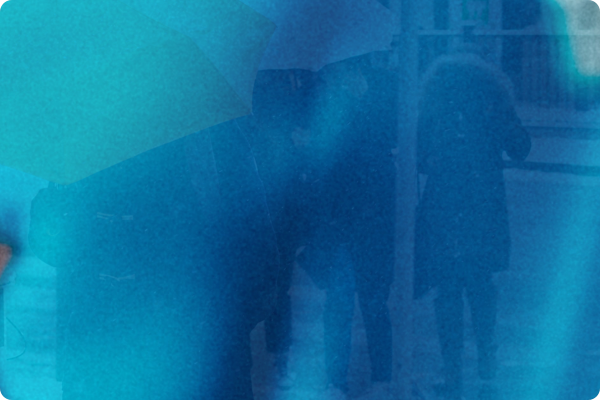