SABIC Innovative Plastics and Azdel, Inc. Launch IXIS Automotive Composites that Skimp on Weight, Not Performance
18 Sep 2008 • by Natalie Aster
TROY, Mich./ -- In the ongoing search for new ways to reduce vehicle weight, automotive OEMs and tiers have been looking for a better alternative to steel, aluminum and thermosets for large, aerodynamic, horizontal body panels. Now, SABIC Innovative Plastics and Azdel, Inc. have launched their new hybrid thermoplastic composite grade, IXISO 157 composite, a continuous glass-fiber-reinforced sandwich composite for automotive horizontal body panels.
IXIS 157 composite is the first product launched using high performance thermoplastic composite (HPPC) technology - which won the 2007 Frost & Sullivan Excellence in Technology award - and provides critical advantages over traditional materials, starting with a 50 percent weight reduction compared to steel. By adopting IXIS thermoplastic composites, automakers can design cost-effective, lightweight and aerodynamic body panels that will help drive the success of fuel-efficient future models. SABIC Innovative Plastics and Azdel, Inc. are featuring IXIS composites today at the Society of Plastic Engineers Automotive Composites Conference & Exhibition here.
"Together with Azdel, we have made tremendous strides with IXIS composites, including the commercialization of our first grade aimed at off-line painting and the excellent progress toward an online paintable product," said Greg Adams, vice president, SABIC Innovative Plastics, Automotive. "We've leveraged our resources around the globe to develop the IXIS materials that have been featured on two of the most successful 'green' concept vehicles in the world: the Chevrolet Volt and the Hyundai QarmaQ. Our investment in these new technologies enables us to continue to provide innovative solutions to address the automotive industry's environmental, performance and cost challenges."
The IXIS composite is composed of a random glass fiber reinforced core with a glass content (by weight) of approximately 50 percent, together with a 0°/90° skins of continuous unidirectional fiber reinforced thermoplastic. The skin material enables a Class A paint finish and dimensional stability, while the core material aids processing and reduces overall material costs.
Half the Weight of Steel and Many Other Benefits
IXIS composites are significantly lighter in weight than steel and thermoset resins, with the potential to make a large contribution to improved fuel efficiency. They also offer important performance benefits, including excellent sound-deadening qualities for a quiet ride and outstanding damage resistance. In comparison to thermosets, which tend to shatter and splinter on impact, and steel, which tends to crumple, IXIS composites rebound, offering better energy absorption for pedestrian safety.
The polypropylene-based 157 grade is designed for off-line painting, and the upcoming 200 grade is intended for online painting and processing through the e-coat process. Both can be recycled. Thanks to a good polymer/glass fiber bond, the material can be granulated and remolded into other engineering applications.
Unlike steel, IXIS composites enable part integration, such as the insertion of antennas into the roof of a vehicle. Although thermosets have been used in this manner, they are heavier and far more difficult to recycle.
Low-Cost Tooling and Low-Energy Production
IXIS composites offer a compelling weight advantage over steel, but that is just the beginning. "With OEM's facing challenges to reduce greenhouse gas emissions and increase fuel economy, IXIS technology is a cost-effective light-weight alternative to steel," said Mike Birrell, director, Exterior Composites, Azdel, Inc. "It is also significantly less expensive than aluminium. Further, because IXIS composites are designed for low-pressure compression molding - a low-energy process - less costly aluminum tools can be used. All these factors add up to a very attractive economic value for automakers and tiers."
Technology Take-off from Aerospace Industry
Fiber-reinforced composites are a widely used technology for the aviation and aerospace industries. With their long history of breakthrough ideas, SABIC Innovative Plastics and Azdel have adapted this technology for automotive applications by leveraging the dimensional stability and high-quality surface finish of continuous, unidirectional glass fiber. In contrast to cut fibers, continuous fibers inhibit thermal movement, helping to reduce expansion and contraction of large, horizontal parts when exposed to sun and temperature extremes.
About SABIC Innovative Plastics
SABIC Innovative Plastics is a leading global supplier of engineering thermoplastics with a 75-year history of breakthrough solutions that solve its customers' most pressing challenges. Today, SABIC Innovative Plastics is a multi-billion-dollar company with operations in more than 25 countries and over 10,500 employees worldwide. The company continues to lead the plastics industry with customer collaboration and continued investments in new polymer technologies, global application development, process technologies, and environmentally responsible solutions that serve diverse markets such as automotive, electronics, building & construction, transportation, and healthcare. The company's extensive product portfolio includes thermoplastic resins, coatings, specialty compounds, film, and sheet. SABIC Innovative Plastics is a wholly owned subsidiary of Saudi Basic Industries Corporation (SABIC), one of the world's top five petrochemicals manufacturers.
About Azdel, Inc.
Azdel manufactures high performance thermoplastic composites designed for both interior and exterior applications across many different industries. Major segments served include automotive, heavy truck, recreational vehicles, industrial, and other transportation applications. Azdel is a wholly owned subsidiary of Hanwha L&C Corporation, part of the Hanwha Group, a diversified conglomerate with over 20,000 employees and 30 affiliated companies. Hanwha has four key business areas: Chemical, Finance & Securities, Distribution and Leisure & Services.
Source: SABIC Innovative Plastics
Analytics & News
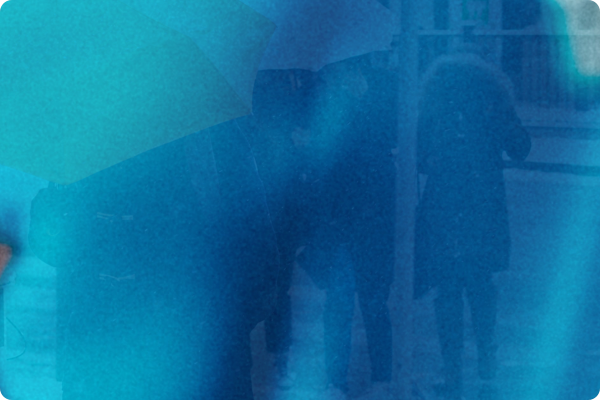